Текстолиты
Текстолиты — это слоистые материалы, получаемые путем прессования уложенной правильными слоями хлопчатобумажной ткани, пропитанной резольными олигомерами или их смесью.
Процесс получения текстолита (рис. 1) состоит из стадии подготовки, пропитки и сушки ткани, сборки и прессования пакетов. Подготовка ткани заключается в сшивании отдельных кусков в непрерывное полотно и наматывании рулонов на оправки. Пропитка и сушка проводятся обычно в вертикальных пропиточно-сушильных машинах.
Пройдя слой пропиточного раствора, ткань через систему отжимных валков, регулирующих содержание связующего, поступает в сушильную камеру машины. Для равномерного высушивания пропитанной ткани температуру в сушильной камере повышают ступенчато от 60 до 140 °С. Количество олигомера и летучих, содержащихся в пропитанных тканях после сушки, составляет соответственно 47—57 и 0,8—2,5% в зависимости от типа ткани и ее назначения.
Важным усовершенствованием в работе пропиточно-сушильных машин является улавливание летучих продуктов, позволяющее повторно использовать ценное сырье — фенол, спирт и значительно улучшить санитарно-гигиенические условия производства.
По выходе из пропиточно-сушильной машины ткань разрезается на листы нужных размеров. Длина и ширина листов определяются в соответствии с габаритами плит пресса. Из нарезанных листов ткани набирают заготовки (пакеты) по наборным коэффициентам, определяющим число слоев ткани, необходимое для образования 1 мм толщины отпрессованного текстолита. Наборный коэффициент зависит от типа пропитанной ткани и содержания связующего.
Для получения текстолита с ровной блестящей поверхностью без вмятин пакеты пропитанной ткани укладывают между полированными листами из нержавеющей стали, на которые ровным слоем наносят смазывающее вещество (олеиновую кислоту, стеарин). Смазку можно вводить и в олигомер после растворения. Таким связующим пропитывают ткань лишь для облицовочных (поверхностных) слоев, которые могут отличаться также и повышенным содержанием связующего.
Пакеты пропитанной ткани загружают между плитами гидравлического пресса, нагретыми до температуры не выше 40 °С. По окончании загрузки создается давление 3—7 МПа и материал прогревается до температуры прессования. После «зарезинивания» олигомера (полный переход в стадию резитола) давление увеличивают до 7—10 МПа. При ступенчатом повышении давления сводятся до минимума потери связующего за счет выжима, предотвращается появление разрывов на поверхности и таким образом обеспечиваются более высокие физико-механические показатели текстолита.
Максимальное давление прессования определяется прочностью наполнителя. Для хлопчатобумажных тканей оно составляет около 10 МПа. Дальнейшее увеличение давления может привести к разрушению структуры ткани и резкому снижению прочности текстолита.
Прогрев до температуры прессования должен обеспечивать равномерное нагревание материала по толщине. Время, необходимое для прогрева, определяется из расчета 1 мин на 1 мм толщины прессуемого материала, однако оно должно быть не менее 25 мин.
Началом выдержки считается момент достижения греющими плитами пресса температуры 150 °С. Время выдержки в прессе под давлением определяется из расчета 3—5 мин на 1 мм толщины прессуемого материала и приближается к верхнему пределу (5 мин/мм) для плит толщиной 30 мм. Поддерживаемая во время выдержки температура 150—165 °С обеспечивает оптимальную скорость отверждения резольных олигомеров.
По окончании выдержки материал охлаждают в прессе под давлением до 40 °С и ниже, после чего давление уменьшают до атмосферного и готовый текстолит выгружают из пресса. Листы текстолита толщиной до 6 мм обрезают гильотинными ножницами, а более толстые плиты — на фрезерных станках.
Свойства текстолитов
Свойства текстолитов зависят от соотношения олигомера и наполнителя. При одном и том же содержании связующего прочность материала тем больше, чем тоньше ткань. По мере увеличения содержания олигомера сверх определенного предела, необходимого для склеивания листов ткани в монолит, прочность текстолита снижается. Для большинства слоистых пластиков максимальная прочность соответствует содержанию связующего около 30%. Однако в текстолитах содержание связующего, как уже указывалось, значительно выше. Это объясняется тем, что при низком содержании связующего возникает необходимость в увеличении давления при прессовании, ухудшаются водостойкость и химическая стойкость материала. Кроме того, высокое содержание ткани в текстолите приводит к удорожанию материала.
Физико-механические текстолитов приведены ниже: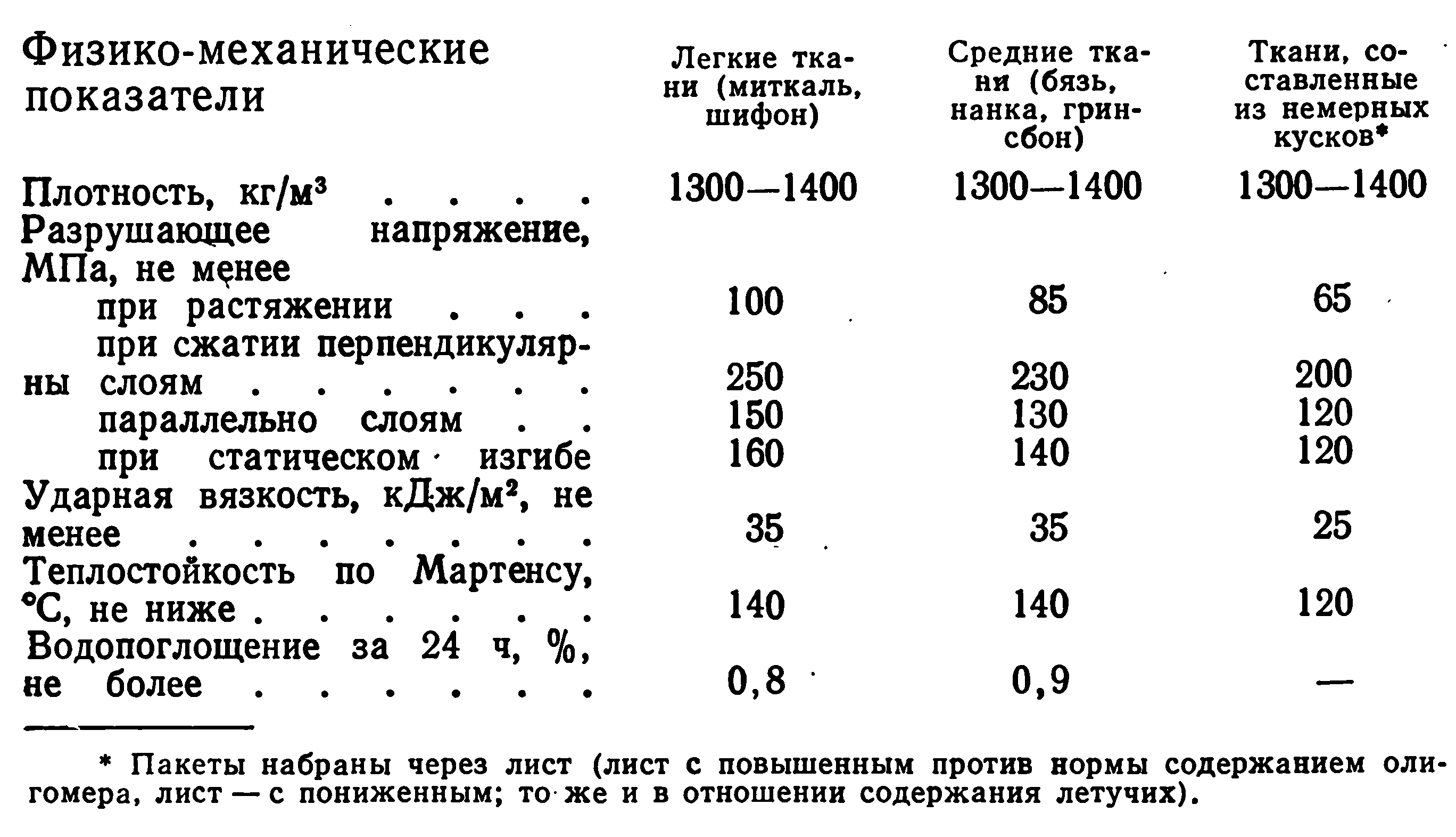
Благодаря высоким физико-механическим показателям, маслобензостойкости и относительно высокой водостойкости текстолиты широко применяется в машиностроении для изготовления прокладочных колец, шестерен, вкладышей подшипников. Текстолитовые вкладыши подшипников для металлургических прокатных станов успешно заменяют бронзовые и служат в несколько раз дольше. Текстолитовые шестерни бесшумны в работе, для них не требуется специальной смазки (в качестве смазки можно использовать воду или водную эмульсию). При работе в паре с металлическими шестерни из текстолитов меньше изнашиваются. Для снижения коэффициента трения и истираемости текстолита, а также для повышения его теплопроводности в состав раствора олигомера, используемого для пропитки ткани, вводят графит.
В электротехнике текстолиты применяют для изготовления электроизоляционных деталей, пазовых клиньев электрических машин, шкивов деталей радиоаппаратуры, панелей и т. д. Температура эксплуатации колеблется от —60 до 60 °С (и выше).
Кузнецов Е. В., Прохорова И. П. Альбом технологических схем производства полимеров и пластических масс на их основе. Изд. 2-е. М., Химия, 1975. 74 с.
Кноп А., Шейб В. Фенольные смолы и материалы на их основе. М., Химия, 1983. 279 с.
Бахман А., Мюллер К. Фенопласты. М., Химия, 1978. 288 с.
Николаев А. Ф. Технология пластических масс, Л., Химия, 1977. 366 с.
Автор: Коршак В.В.
Источник: Коршак В.В., Технологии пластических масс, 3-е издание, 1985 год
Дата в источнике: 1985 год