Двигатель из полимеров уже не за горами!
Двигатель из полимеров не такая уже и фантастика! Использование композитов на полимерной основе находит все большее применение в автомобилестроении, позволяя уменьшить вес транспортных средств и повысить их эффективность. По оценкам экспертов автомобили будущего будут на 75% состоять из различного вида полимерных материалов. Новый и довольно успешный шаг в этом направлении сделала международная группа исследователей из Германии и Японии.
Группа разработчиков новых приводных систем (NAS) из исследовательского центра Fraunhofer ICT (Германия), совместно со специалистами Sumitomo Bakelite Co. Ltd. (Япония) разработали облегченный корпус блока цилиндров на основе армированных волокном композиционных материалов.
Автомобили должны стать легче, чтобы достигнуть уменьшения объемов потребляемого топлива. На сегодняшний день, для изготовления корпуса автомобиля и приводного механизма используются металлы, использование армированного пластика может снизить вес среднестатистического автомобиля на 20%. Современные технологии уже позволяют наладить серийное производство авто компонентов из пластика, методом литья.
На сегодняшний день полимеры, как материал для изготовления автомобиля, уже «проникли» во многие детали и компоненты, но в вопросе изготовления двигателей и трансмиссии по-прежнему доминируют металлы, чем блокируют дальнейшее снижение веса транспортных средств. Определенного успеха, в вопросе автомобильного «похудания», помогло достигнуть – использование алюминия, но применение волоконно-армированных пластиков сулит еще большими успехами.
Мы использовали волоконно-армированный композиционный материал, чтобы создать корпус блока цилиндров для экспериментального одно-цилиндрового двигателя,
сообщил, руководитель проекта Доктор Ларс-Фредрик Берг, возглавляющий в Fraunhofer группу по исследованию новых приводных систем (NAS). Кроме того, Берг заметил:
Полученный корпус цилиндра весит примерно на 20 процентов меньше, чем аналог из алюминия, при той же цене!
Идея применения композиционных материалов – проста, но не так просты технологические решения, позволяющие реализовать подобную идею на практике. К материалам, применяемым в автопроизводстве, предъявляются довольно высокие требования. Они (материалы) должны выдерживать, не повреждаясь, экстремальные вибрации, температуры и высокое давление. Еще в 80-х годах прошлого века было обнаружено, что пластики могут соответствовать упомянутым требованиям. Тем не менее, серийное производство автомобильных деталей из полимеров не представлялось возможным в те времена. Причин тому – обширное использование ручного труда, что вело к увеличению себестоимости и ограниченности объемов поставок. Это при том, что такой элемент автомобиля, как блок цилиндров из металла изготавливается в многомиллионном объеме.
Исследователям из NAS потребовалось много времени, чтобы убедиться в прочности двигателя после применения новых композиционных материалов на полимерной основе.
Первым делом, мы изучили участки в конструкции двигателя, что в наибольшей степени подвержены воздействию высоких температурных и механических нагрузок. В таких местах мы используем металлические вставки для усиления износостойкости,
– объясняет Ларс-Фредрик Берг.
Один из таких элементов, обнаруженных командой исследователей, – гильза цилиндра. Поршень внутри этого цилиндра перемещается миллионы раз во время движения автомобиля. В результате, разработчики изменили геометрию ряда компонентов таким образом, чтобы минимизировать воздействия термических нагрузок на пластмассовые компоненты.
К пластикам, задействованным в разработке двигателя, применяется целый комплекс требований. Они должны обладать необходимой жесткостью и твердостью, а также должны быть устойчивы к воздействию бензина, масел и гликоля в охлаждающей жидкости. Применяемый пластик должен обладать коэффициентом теплового расширения не превышающим показатели металла, а также, должен обладать хорошей адгезией по отношению к металлу.
Эксперименты показали, что если коэффициент теплового расширения пластмассовых компонентов превышал показатель компонентов из металла – они начинали расслаиваться. Исследовательский центр SBHPP компании Sumitomo Bakelite пришел на помощь в решении этой проблемы. Специалисты SBHPP разработали армированный стекловолокном композиционный материал на основе фенопластов (wiki.MPlast.by). Итоговая композиция на 45% состоит из смолы и на 55% – из волокна. Получившийся в результате материал имеет достаточные свойства, чтобы реализовать поставленную Fraunhofer задачу. Следует также заметить, что применение углеродного волокна позволило бы сделать агрегат еще легче, но дороговизна такого материала заставляет задуматься: Что приоритетнее? Вес или цена будущего автомобиля?
В результате, разработчики использовали инновационный материал в гранулированном виде и литье под давлением, как метод производства. Форма, в которую попадает расплавленный материал, была специально разработана при помощи компьютерного моделирования. Следует отметить, что подобный метод производства авто компонентов позволяет быстро получать готовое изделие, практически не требующее дополнительной обработки, в то время как детали из алюминия должны проходить целую серию производственных операций. Тем самым, новая технология может впервые открыть композиционные материалы для крупносерийного производства.
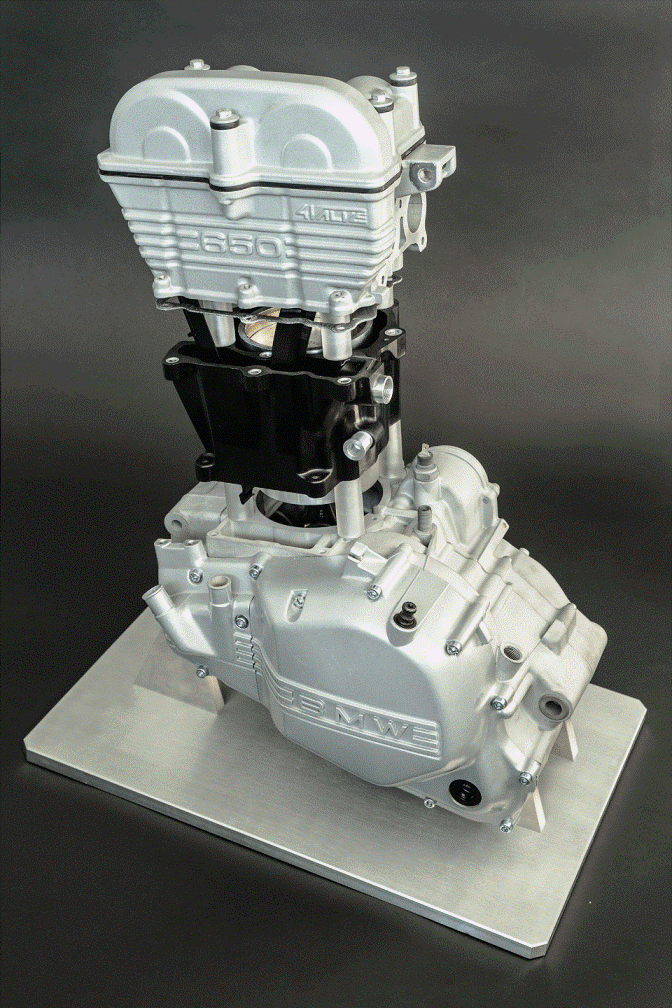
Демонстрационная модель экспериментального двигателя с облегченным корпусом коробки цилиндров (Фото: Fraunhofer ICT)
Исследовательская группа уже провела успешные тестовые испытания нового двигателя! Доктор Берг так прокомментировал полученные результаты:
Мы доказали, что он [двигатель, ред. MPlast.by] способен обеспечить такую же производительность, как и двигатель, построенный по традиционным технологиям!
Помимо решения задачи по уменьшению веса, новый двигатель, изготовленный с использованием полимерных композитов, обладает и более низкими (чем алюминиевый «собрат») уровнем шума и уровнем выбросов. Увидеть новинку можно будет на предстоящей выставке Hannover Messe 2015, что пройдет с 13 по 17 апреля в Германии. Стенд Fraunhofer ICT будет находиться в павильоне №2 (место C16).
Следует отметить, что первый успех вдохновил международную группу разработчиков. Теперь исследователи планируют пошатнуть гегемонию металла и в других узлах и агрегатах автомобили.
Fraunhofer ICT (Институт химических технологий имени Фраунгофера) – был основан в 1949 году и назван в честь выдающегося ученого и предпринимателя Иозефа Фраунгофера (1787-1826). Штаб-квартира центра расположена в Мюнхене.
Если в начале своей работы офис центра состоял из 3 сотрудников, сегодня Fraunhofer ICT – крупнейший научно-исследовательский центр прикладных исследований в Европе. Области исследований центра ориентированы на потребности людей: здоровье, безопасность, коммуникации, энергетика и окружающая среда.